All Categories
all-categories
Preloaded, low-friction ball screw
High-resolution high-load linear actuator. Stepper motor for high torque. Highly dynamic, closed-loop DC and BLDC motors for high velocities. Robust design for industrial environments.
Application fields
Research. Automation. Optical alignment. /Asset/csm_L-239-50SD_5074781c2a.jpg
Highest precision with PIOne linear encoder: Minimum incremental motion 0.5 nm
High guiding accuracy
Compact design with 160 mm width
Reference-class linear stage
Thanks to the smooth-running precision linear guides with crossed roller bearings, the linear stage is particularly suitable for scanning applications with constant velocity. The anti-creep system reliably prevents cage creep. The guides have high load capacity and high precision under all operating conditions.
PIMag® magnetic direct drive
3-phase magnetic direct drives do not use mechanical components in the drivetrain, they transmit the drive force to the motion platform directly and without friction. The drives reach high velocities and accelerations. Ironless motors are particularly suitable for positioning tasks with the highest demands on precision because there is no undesirable interaction with the permanent magnets. This allows smooth running even at the lowest velocities and at the same time, there is no vibration at high velocities. Nonlinearity in control behavior is avoided and any position can be controlled easily. The drive force can be set freely.
Direct position measuring
Position measuring is performed with the highest accuracy directly at the motion platform so that nonlinearity, mechanical play or elastic deformation have no influence on position measuring.
The high-resolution PIOne encoder was developed by PI and, with corresponding processing of the measured values, allows a position resolution of much less than one nanometer. The optical and noncontact PIOne encoders are based on an interferometric measuring principle. Due to the short signal period and the high quality of the signals, the linearity error of PIOne encoders is less than 1 %. PIOne encoders support direction sensing when evaluating a reference signal.
Absolute encoders supply explicit position information that enables immediate determination of the position. This means that referencing is not required during switch-on, which increases efficiency and safety during operation.
Fields of application
Industry and research. Automation, measuring technology, photonics and precision scanning in semiconductor or flat panel display manufacturing /Asset/V-551 Precision Linear Stage.jpg
Crossed roller guides for high load capacity
Iron core or ironless PIMag® linear motor developed by PI
Flexible adaption
The construction allows flexible adaption to the requirements. Technically sophisticated and cost-critical applications can be equally served with different travel ranges, drives, and measuring systems. XY assemblies are also possible
PIMag® linear motor
Linear motors are electromagnetic direct drives. They dispense with mechanical components in the drivetrain and transfer the drive force directly and friction-free to the motion platform. The drives reach high velocities and accelerations.
Ironless motors are particularly suitable for positioning tasks with the highest demands on precision because there is no undesirable interaction with the permanent magnets. This allows smooth running even at the lowest velocities and at the same time, there is no vibration at high velocities. Nonlinearity in control behavior is avoided and any position can be controlled easily. The drive force can be set freely.
Iron core motors are used when forces and accelerations need to be achieved in a limited installation space. The design with iron cores maximizes the magnetic forces and ensures high thermal stability of the drive.
PIMag®
PI develops proprietary magnetic motors if positioning systems need to achieve specific performance characteristics that cannot be reached by using drive components currently available on the market, for example, to achieve a high force density or a compact design. The motors developed by PI are identified by the PIMag® brand name.
Crossed roller guide
With crossed roller guides, the point contact of the balls in ball guides is replaced by line contact of the hardened rollers. Consequently, they are considerably stiffer and need less preload, which reduces friction and allows smoother running. Crossed roller guides are also distinguished by high guiding accuracy and load capacity. Force-guided rolling element cages prevent cage creep.
Direct position measuring
Position measuring is performed with the highest accuracy directly at the motion platform so that nonlinearity, mechanical play, or elastic deformation have no influence on position measuring.
Application fields
Industry and research. Measuring technology, photonics and precision scanning in semiconductor or medicine technology. /Asset/csm_V-508_588271805f.jpg
Ideal for scanning applications or high-precision positioning
Cleanroom compatible
PIglide positioning systems have a magnetic linear motor, magnetically preloaded air bearings and an optical linear encoder: Noncontact and friction-free motion for the highest accuracy and reliability
Application fields
PIglide positioning systems are ideally suited for many high-precision applications such as metrology, photonics, and precision scanning in semiconductor or flat panel display manufacturing.
Thanks to the friction-free motion, no particles are formed, which makes PIglide stages ideal for cleanroom applications. /Asset/csm_A-110_PIC_9106d68816.jpg
Compact linear stage with low-backlash drive screw and ball guides. Directly mountable XY combination. Integrated reference point and limit switches: Hall effect.
The linear stage is available in two design variants:
Noncontact optical encoders measure the position directly at the platform with the greatest accuracy. Nonlinearity, mechanical play or elastic deformation have no influence on the measurement.
Drive types
Application fields
Medical industry, Autofocus, Precision microassembly, Biotechnology, Automation /Asset/csm_L-505-02-2er-9_5_46f8d6fc0a.jpg
Covering strip on the side for protection against particles
Reference-class linear stage
A new linear stage family with linear motors expands PI's product portfolio for industrial solutions. High-performance ironless linear motors, heavy-duty recirculating ball bearings, and precision linear encoders are used. The covering strip on the side and the purge air connection prevent contamination by particles.
Pioneering design
Compared to the competition, the recirculating ball bearings of the V-417 series offer a higher load capacity and allow higher dynamics. The high resolution of the encoders allows improved tracking performance, smaller tracking error, and improved settling times. For maximum flexibility, it is possible to choose between incremental and absolute encoders. Absolute encoders supply explicit position information that enables immediate determination of the position. This means that referencing is not required during switch-on, which increases efficiency and safety during operation.
Linear motors
Linear motors are electromagnetic direct drives. They dispense with mechanical components in the drivetrain and transfer the drive force directly and friction-free to the motion platform. The drives reach high velocities and accelerations. Ironless motors are particularly suitable for positioning tasks with the highest demands on precision because there is no undesirable interaction with the permanent magnets. This allows smooth running even at the lowest velocities and at the same time, there is no vibration at high velocities. Nonlinearity in control behavior is avoided and any position can be controlled easily. The drive force can be set freely.
Application fields
Laser cutting. Scanning. Digital printing. Electronics assembly and inspection. AOI (Automatic Optical Inspection). Automation. Flat screen manufacturing. Applications with high demands on dynamics, precision, smooth scan motion, short settling times, and low tracking error. /Asset/csm_V-417-096211E1-2500_c5e5d83771.jpg
Covering strip on the side for protection against particles
Powerful linear stage for use in demanding industrial applications
Precision ball screws, high-performance synchronous servo motors, heavy-duty recirculating ball bearings, and precision rotary and linear encoders enable continuous and reliable operation under high load. The optional holding brake allows use as Z axis. The ball screw can be relubricated from the outside without disassembling to ensure high reliability and long lifetimes. It is also possible to integrate into a customer's central lubrication system. The covering strip on the side and the purge air connector prevent contamination by particles.
Pioneering design
The recirculating ball bearings of the L-417 series are designed for high load capacity and dynamics. The high resolution of the motors allows improved tracking performance, smaller tracking error, and improved settling times.
Synchronous servo motor
These motors have high positioning accuracy and high overload capacity over a large rotation speed range. High torque and low inertia ensure the high dynamics of the drives. The long lifetime, high performance, and robustness of these motors allow excellent results in industrial automation applications.
Application fields
Laser cutting. Electronics production. AOI (Automatic Optical Inspection). Automation. Applications with high demands on dynamics, precision, smooth motion, short settling times, and low tracking errors. /Asset/csm_PI-L-417-059232-2500_aa629c82da.jpg
Noncontact optical encoders measure the position directly at the platform with the greatest accuracy. Nonlinearity, mechanical play or elastic deformation have no influence on the measurement. Optical limit and reference switches. Further travel ranges on request.
Crossed roller guide
With crossed roller guides, the point contact of the balls in ball guides is replaced by line contact of the hardened rollers. Consequently, they are considerably stiffer and need less preload, which reduces friction and allows smoother running. Crossed roller guides are also distinguished by high guiding accuracy and load capacity. Force-guided rolling element cages prevent cage creep.
Fields of application
Medical industry. Laser cutting. Biotechnology. Metrology. Laser marking. /Asset/csm_L-741-131111_fada1ba831.jpg
Ideal for scanning applications or high-precision positioning
Cleanroom compatible
Low profile
The high-precision PIglide IS XY planar scanner with air bearing has a flat design and is an alternative to the stacked XY stages. The efficient, compact design saves space in machines with limited installation space.
PIMag® magnetic direct drive
3-phase magnetic direct drives do not use mechanical components in the drivetrain, they transmit the drive force to the motion platform directly and without friction. The drives reach high velocities and accelerations. Ironless motors are particularly suitable for positioning tasks with the highest demands on precision because there is no undesirable interaction with the permanent magnets. This allows smooth running even at the lowest velocities and at the same time, there is no vibration at high velocities. Nonlinearity in control behavior is avoided and any position can be controlled easily. The drive force can be set freely.
Operation with digital controllers from leading manufacturers offers advanced control algorithms for improving the dynamics and error compensation.
Application fields
PIglide positioning systems are ideally suited for high-precision applications, such as inspection systems, laser marking, microscopy or scanning. /Asset/csm_A-311_PIC_2e093ee442.jpg
Cleanroom compatible
Three performance classes: Base, Plus, and Ultra
PIglide reference-class XY positioning system
The PIglide HS planar scanner has magnetic linear motors, vacuum preload, and an absolute encoder: Contact- and friction-free motion for the highest accuracy and reliability.
The positioning system was designed to maximize the throughput and ensure the highest precision. Flexible coupling of the bridge axis to the gantry axis allows lateral decoupling without sacrificing the stiffness of the system.
The A-322 is coupled with industry-leading controllers and drive modules from ACS that offer superior servo performance, advanced control algorithms to improve dynamic performance and error compensation, and a wide suite of software development tools.
The A-322 series is a starting point for further adaptations. Critical core components such as linear motors, measuring systems, and air bearing assemblies have already been developed, tested, and have proven their capabilities. Depending on the application and requirements of the customer, a variant of the A-322 series forms the ideal starting point for a tailor-made, ultraprecise solution.
Absolute encoder
Absolute encoders supply explicit position information that enables immediate determination of the position. This means that referencing is not required during switch-on, which increases efficiency and safety during operation.
PIMag® magnetic direct drive
3-phase magnetic direct drives do not use mechanical components in the drivetrain, they transmit the drive force to the motion platform directly and without friction. The drives reach high velocities and accelerations. Ironless motors are particularly suitable for positioning tasks with the highest demands on precision because there is no undesirable interaction with the permanent magnets. This allows smooth running even at the lowest velocities and at the same time, there is no vibration at high velocities. Nonlinearity in control behavior is avoided and any position can be controlled easily. The drive force can be set freely.
Long lifetime, cleanroom compatible drag chains
The A-322 has high-quality, long-lasting ribbon cables and pneumatic hoses. Extensive research and development has resulted in an optimized cable management system that enables millions of maintenance-free cycles. Teflon coating ensures low particle formation.
Application fields
PIglide positioning systems are ideally suited for many high-precision applications, such as metrology, photonics, and precision scanning as well as in semiconductor or flat panel display manufacturing.
Thanks to the friction-free motion, no particles are formed, which makes PIglide stages ideal for cleanroom applications. /Asset/csm_A-322_PIC_5651517613.jpg
Hybrid design: Gantry axis with recirculating ball bearing guides, bridge axis with air bearing
Absolute encoder
High-performance ironless linear motors
Various travel ranges. Options and customized adaptations
Flexible modular platform
The A-341 PIglide HGS hybrid gantry system was developed for applications that require overhead motion and long travel ranges.
The A-341 hybrid gantry has a unique hybrid guide design. The bridge axis is equipped with a friction-free guide with air bearings that allow exact control of velocity as well as outstanding repeatability and straightness. The guide with air bearings considerably reduces particle emission over the workspace. The gantry axis is equipped with recirculating ball bearing guides on both sides for robustness and precision in limited installation space.
This combination of different guide technologies means that the A-341 hybrid gantry is ideally suited to applications that are based on the step-and-scan principle and at the same time, require a compact design.
The A-341 is coupled with industry-leading controllers and drive modules from ACS that offer superior servo performance, advanced control algorithms to improve dynamic performance and error compensation, and a wide suite of software development tools.
PIMag® magnetic direct drive
3-phase magnetic direct drives do not use mechanical components in the drivetrain, they transmit the drive force to the motion platform directly and without friction. The drives reach high velocities and accelerations. Ironless motors are particularly suitable for positioning tasks with the highest demands on precision because there is no undesirable interaction with the permanent magnets. This allows smooth running even at the lowest velocities and at the same time, there is no vibration at high velocities. Nonlinearity in control behavior is avoided and any position can be controlled easily. The drive force can be set freely.
Application fields
Scanning, Digital printing, Electronics assembly and inspection, AOI (Automatic Optical Inspection), Automation.
Absolute encoder
Absolute encoders supply explicit position information that enables immediate determination of the position. This means that referencing is not required during switch-on, which increases efficiency and safety during operation. /Asset/csm_A-341_2500px_27b33165e6.jpg
Overhead moving XY gantry
Precision recirculating ball bearing guides
Absolute encoder
High-performance ironless linear motors
Various travel ranges. Options and customized adaptations
Flexible modular platform
The MGS gantry system has been designed to maximize throughput for applications requiring overhead motion. This stage is ideal for 3D printing, assembly, pick-and-place, alignment, inspection, and industrial automation applications.
The MGS uses preloaded linear mechanical bearings which are designed to provide optimized stiffness and precision. Optional stainless steel guide rails can be delivered.
The gantry axis incorporates dual linear motors and dual linear encoders. Ironless linear motors provide smooth motion and no cogging or attractive forces. The linear motor and linear encoders are noncontact devices, so there is no backlash, wear, or maintenance concerns.
The A-351 is coupled with industry-leading controllers and drive modules from ACS that offer superior servo performance, advanced control algorithms to improve dynamic performance and error compensation, and a wide suite of software development tools.
Application fields
Scanning, Digital printing, Electronics assembly and inspection, AOI (Automatic Optical Inspection), Automation. /Asset/csm_A-351_d87dd33a4a.jpg
Stepper motors and closed-loop DC motors
Optional: Linear encoder for direct position measuring
Crossed roller guides
Noncontact reference and limit switches
Compact Z stage, versatile in use
Z stage with compact size due to folded drive with belt drive. Fits onto linear stages with M6 50 mm x 50 mm connection spacing (e.g., L-406).
Crossed roller guide
With crossed roller guides, the point contact of the balls in ball guides is replaced by line contact of the hardened rollers. Consequently, they are considerably stiffer and need less preload, which reduces friction and allows smoother running. Crossed roller guides are also distinguished by high guiding accuracy and load capacity. Force-guided rolling element cages prevent cage creep.
Highly accurate position measuring with incremental linear encoder
Noncontact optical encoders measure the position directly at the platform with the greatest accuracy. Nonlinearity, mechanical play or elastic deformation have no influence on the measurement.
Fields of application
Research, Semiconductor technology, Photonics, Automation /Asset/csm_L-306-011100_c2e59b73ad.jpg
High-resolution encoder
DC, BLDC, and stepper motors
Zero-play ball screw
Vacuum-compatible items available
Precision-class Z stage
High guiding accuracy and stiffness due to ball screws and crossed roller guides. Stress-relieved aluminum base for highest stability. Vacuum-compatible product variants on request. Noncontact limit and reference switches (Hall effect). Reference switch with direction sensing in the middle of the travel range.
Minimum incremental motion and slow motion
In conjunction with the SMC Hydra controller, versions with stepper motor and integrated linear encoder (L-310.xASD) achieve repeatable minimum incremental motion in the range of the sensor resolution. The same configuration achieves constant low velocities of a few sensor increments per second.
Highly accurate position measuring with incremental linear encoder
Noncontact optical encoders measure the position directly at the platform with the greatest accuracy. Nonlinearity, mechanical play or elastic deformation have no influence on the measurement.
Application fields
Precision positioning in industry and research, high duty cycles. /Asset/csm_L-310_PIC_c9118711be.jpg
Deep groove ball bearings provide high load capacity and long lifetime
Clear aperture for transmitted-light applications
High velocity and acceleration
PIMag® magnetic direct drive
3-phase magnetic direct drives do not use mechanical components in the drivetrain, they transmit the drive force to the motion platform directly and without friction. The drives reach high velocities and accelerations. Iron core motors are used when forces and accelerations need to be achieved in a limited installation space. The design with iron cores maximizes the magnetic forces and ensures high thermal stability of the drive.
Application fields
Medical industry. Sample inspection. Precision microassembly. Research. Biotechnology. Semiconductor technology. Metrology. Automation. /Asset/csm_PI_V-611-998061_e5f5e8d04d.jpg
Cleanroom compatible
Can be mounted vertically or horizontally
The PIglide RM series of motorized rotation stages are designed for accuracy, precision, high stiffness, and ease of use, and can be mounted in any orientation.
Various options can be combined to create a solution ideal for point-to-point indexing or constant velocity scanning.
The RM stages offer superior travel accuracy, flatness, and wobble performance. Because they are friction free and require no maintenance or lubrication, they are ideal for use in cleanrooms.
Absolute encoder (optional)
Absolute encoders supply explicit position information that enables immediate determination of the position. This means that referencing is not required during switch-on, which increases efficiency and safety during operation.
Application fields
Optical alignment, metrology, inspection systems, calibration, scanning. /Asset/csm_A-62x_560dce6cdb.jpg
Option for self-locking at rest by magnetic preload
The directly driven low-profile rotation stages of the PIglide RL series are designed for the highest precision with low-profile design. Various options can be combined to create a solution ideal for point-to-point indexing or constant velocity scanning. The RL stages offer superior travel accuracy, flatness, and wobble performance.
Absolute encoder (optional)
Absolute encoders supply explicit position information that enables immediate determination of the position. This means that referencing is not required during switch-on, which increases efficiency and safety during operation.
Application fields
Optical alignment, wafer inspection, wafer alignment, measuring technology, inspection systems, calibration, scanning.
Thanks to the friction-free motion, no particles are formed, which makes PIglide stages ideal for cleanroom applications. /Asset/csm_A-637_PIC_fb527a7bf0.jpg
Positions larger loads quickly and with precision
Self-locking when switched off: Saves energy and reduces generation of heat
Central aperture for more fields of application
Precision-class rotation stage
PILine® stages are particularly suitable for applications that require fast precision positioning. When switched off, the self-locking drive holds the position of the stage mechanically stable. Energy consumption and heat generation are therefore considerably reduced. Applications with a low duty cycle that are battery-powered or heat-sensitive benefit from these characteristics. The position of the axis is measured by an encoder and an optical reference switch allows reliable repeatable motion. The piezomotor drive principle and its electrical operation are inexpensive and can be customized.
Highly accurate position measuring with incremental encoder
Noncontact optical encoders measure the position directly at the platform with the greatest accuracy. Nonlinearity, mechanical play, or elastic deformation have no influence on the measurement.
Fields of application
Micromanipulation, automation, biotechnology, sample manipulation, sample positioning, optical metrology, vacuum applications to 10-6 hPa (optional)
PILine® ultrasonic piezomotors
An integral part of a PILine® ultrasonic piezomotor is a piezo actuator that is preloaded against a movable, guided runner via a coupling element. The piezoceramic actuator is excited to ultrasonic oscillation by a high-frequency AC voltage between 100 and 200 kHz. Deformation of the actuator leads to periodic diagonal motion of the coupling element relative to the runner. The feed created is a few nanometers per cycle; the high frequencies lead to the high velocities. Preloading the piezoceramic actuator against the runner ensures self-locking of the drive when at rest and switched off.
Crossed roller guide
With crossed roller guides, the point contact of the balls in ball guides is replaced by line contact of the hardened rollers. Consequently, they are considerably stiffer and need less preload, which reduces friction and allows smoother running. Crossed roller guides are also distinguished by high guiding accuracy and load capacity. Force-guided rolling element cages prevent cage creep. /Asset/csm_PI_U-651-04_klein_0063908701.jpg
Self-locking when switched off: Saves energy and reduces generation of heat
Central aperture for more fields of application /Asset/csm_PI_U-628_02_d8da36f5c6.jpg
Extremely space-saving
Positions small loads quickly and with precision
Self-locking when switched off: Saves energy and reduces generation of heat
Light and low noise
Precision-class rotation stage
PILine® stages are particularly suitable for applications that require fast precision positioning. When switched off, the self-locking drive holds the position of the stage mechanically stable. Energy consumption and heat generation are therefore considerably reduced. Applications with a low duty cycle that are battery-powered or heat-sensitive benefit from these characteristics. The position of the axis is measured by an encoder and an optical reference switch allows reliable repeatable motion. The piezomotor drive principle and its electrical operation are inexpensive and can be customized.
Highly accurate position measuring with incremental encoder
Noncontact optical encoders measure the position directly at the platform with the greatest accuracy. Nonlinearity, mechanical play or elastic deformation have no influence on the measurement.
PILine® ultrasonic piezomotor
An integral part of a PILine® ultrasonic piezomotor is a piezo actuator that is preloaded against a movable, guided runner via a coupling element. The piezoceramic actuator is excited to ultrasonic oscillation by a high-frequency AC voltage between 100 and 200 kHz. Deformation of the actuator leads to periodic diagonal motion of the coupling element relative to the runner. The feed created is a few nanometers per cycle; the high frequencies lead to the high velocities. Preloading the piezoceramic actuator against the runner ensures self-locking of the drive when at rest and switched off.
Fields of application
Micromanipulation, Automation, Biotechnology, Sample manipulation, Sample positioning, optical metrology /Asset/csm_PI_U-622_1180fb125e.jpg
Option: Direct position measurement with angle measuring system
Combination with WT-90 with common pivot point
Precision-class goniometer stage
Polished and hardened worm drive with high gear ratio for precision positioning. Two adjustable limit switches.
Can be combined with WT-90 for 2-axis motion with common pivot point.
Application fields
Precision microassembly, Metrology, Photonics, Optical alignment /Asset/csm_WT-120_9baf470bdd.jpg
Combination with WT-85 with common pivot point
Precision-class goniometer stage
Drive with high gear ratio for precision positioning. Two limit switches. Large clear aperture with 60 mm x 25 mm.
Can be combined with WT-85 for 2-axis motion with common pivot point.
Application fields
Precision microassembly, Metrology, Photonics, Optical alignment. /Asset/csm_WT-100_PIC_ebcd45e175.jpg
Robust industrial design for a long lifetime
High-precision incremental or absolute linear encoder
Ideal for gantry systems
Compact industrial design for applications with low power requirements
The V-855 is a heavy-duty and highly dynamic linear stage for industrial applications. Its design is consistently geared to demanding industrial conditions and it is characterized by high stiffness and the use of high-quality components: recirculating ball bearing guides, 3-phase linear motor, incremental or absolute linear encoder. The high resolution of the encoders allows an excellent tracking performance, small tracking errors, and short settling times. Industry-compatible connectors offer a fast and secure connectivity. The optional motion platform offers versatile assembly options with a triple M6 hole pattern.
Linear motor with direct drive
3-phase magnetic direct drives do not use mechanical components in the drivetrain, they transmit the drive force to the motion platform directly and without friction. The drives reach high velocities and accelerations. Ironless motors are particularly suitable for positioning tasks with the highest demands on precision because there is no undesirable interaction with the permanent magnets. This allows smooth running even at the lowest velocities and at the same time, there is no vibration at high velocities. Nonlinearity in control behavior is avoided and any position can be controlled easily. The drive force can be set freely.
Application fields
Electronics assembly: Sensor and camera assembly. Noncontact inspection, X-ray inspection, and AOI (automated optical inspection). Sensor and ultrasonic tests. Semiconductor manufacturing: Wafer processing and inspection. Laser machining: Laser welding. Highly dynamic applications in precision automation, smooth scan motion, minimum tracking errors, and short settling times. /Asset/csm_V-855_merged-tif_Bilder-Web_196244dcfc.jpg
Robust industrial design for a long lifetime
Fast integration thanks to reference edge, easily XY stackable
Creation and delivery of test reports as a standard
Industrial design for high performance and high load
With the V-817, PI has a linear stage in its portfolio for industrial solutions that has a high load capacity and high dynamics. Its design is consistently geared to demanding industrial conditions and it is characterized by high stiffness and the use of high-quality components: Recirculating ball bearing guides, 3-phase linear motor, incremental linear encoder. The high resolution of the encoders allows an excellent tracking performance, small tracking errors, and short settling times. Industry-compatible connectors offer a fast and secure connectivity. The optional motion platform offers versatile assembly options with a triple M6 hole pattern. A particularly low overall height is achieved without this platform, which offers advantages especially in XY combinations.
Linear motor with direct drive
3-phase magnetic direct drives do not use mechanical components in the drivetrain, they transmit the drive force to the motion platform directly and without friction. The drives reach high velocities and accelerations. Ironless motors are particularly suitable for positioning tasks with the highest demands on precision because there is no undesirable interaction with the permanent magnets. This allows smooth running even at the lowest velocities and at the same time, there is no vibration at high velocities. Nonlinearity in control behavior is avoided and any position can be controlled easily. The drive force can be set freely.
Fully integrated multi-axis systems
The V-817 linear stages are perfectly suited for being integrated into complex systems. Therefore, PI offers integrated XY or XYZ multi-axis systems with the suitable controller as well as accessories such as a granite base, machine frame, mounting adapter, cable set, and appropriate software support. For requests regarding multi-axis systems, contact our sales department.
Application fields
Electronics assembly: Sensor and camera assembly. Noncontact inspection, X-ray inspection, and AOI (automated optical inspection). Sensor and ultrasonic tests. Semiconductor manufacturing: Wafer processing and inspection. Laser machining: Laser welding. Highly dynamic applications in precision automation, smooth scan motion, minimum tracking errors, and short settling times. /Asset/csm_V-817-336211E0-tif_Bilder-Web_f4dd3928ba.jpg
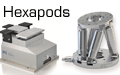
Motorized Positioning Stages, Actuators, Motor Controllers
/Asset/hexapods-motorized-micropositioning.gif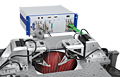
Fiber Alignment Stages / Photonics Alignment
/Asset/PI_F-712_NxM_Axis_Alignment_print_V1_nobkgrnd.png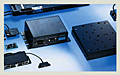
Ceramic Linear Motors: PILine Ultrasonic Motors, Nexline PiezoWalk Nano-Drivers
/Asset/ceramic linear motos.jpg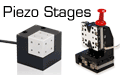
Nanopositioning: Piezo Stages,Actuators, Piezo Controllers, Sensors
/Asset/Piezo-Driven-Nanopositioning.gif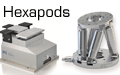
Micropositioning:Motorized Positioning Stages, Hexapods, Controllers
/Asset/hexapods-motorized-micropositioning.gif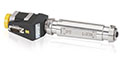
L-239 High-Load Motorized Linear Actuators, High Precision
(4) Dynamic, high-resolution precision drive with dc or stepper motorPreloaded, low-friction ball screw
High-resolution high-load linear actuator. Stepper motor for high torque. Highly dynamic, closed-loop DC and BLDC motors for high velocities. Robust design for industrial environments.
Application fields
Research. Automation. Optical alignment. /Asset/csm_L-239-50SD_5074781c2a.jpg
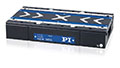
V-551 PIMag® Ultra-High Precision Linear Motor Linear Translation Stage
(3) High velocity and precision due to magnetic direct driveHighest precision with PIOne linear encoder: Minimum incremental motion 0.5 nm
High guiding accuracy
Compact design with 160 mm width
Reference-class linear stage
Thanks to the smooth-running precision linear guides with crossed roller bearings, the linear stage is particularly suitable for scanning applications with constant velocity. The anti-creep system reliably prevents cage creep. The guides have high load capacity and high precision under all operating conditions.
PIMag® magnetic direct drive
3-phase magnetic direct drives do not use mechanical components in the drivetrain, they transmit the drive force to the motion platform directly and without friction. The drives reach high velocities and accelerations. Ironless motors are particularly suitable for positioning tasks with the highest demands on precision because there is no undesirable interaction with the permanent magnets. This allows smooth running even at the lowest velocities and at the same time, there is no vibration at high velocities. Nonlinearity in control behavior is avoided and any position can be controlled easily. The drive force can be set freely.
Direct position measuring
Position measuring is performed with the highest accuracy directly at the motion platform so that nonlinearity, mechanical play or elastic deformation have no influence on position measuring.
The high-resolution PIOne encoder was developed by PI and, with corresponding processing of the measured values, allows a position resolution of much less than one nanometer. The optical and noncontact PIOne encoders are based on an interferometric measuring principle. Due to the short signal period and the high quality of the signals, the linearity error of PIOne encoders is less than 1 %. PIOne encoders support direction sensing when evaluating a reference signal.
Absolute encoders supply explicit position information that enables immediate determination of the position. This means that referencing is not required during switch-on, which increases efficiency and safety during operation.
Fields of application
Industry and research. Automation, measuring technology, photonics and precision scanning in semiconductor or flat panel display manufacturing /Asset/V-551 Precision Linear Stage.jpg
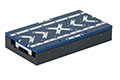
V-508 Precision Direct-Drive Linear Motor Slides
(6) Incremental or absolute linear encoder, various resolutionsCrossed roller guides for high load capacity
Iron core or ironless PIMag® linear motor developed by PI
Flexible adaption
The construction allows flexible adaption to the requirements. Technically sophisticated and cost-critical applications can be equally served with different travel ranges, drives, and measuring systems. XY assemblies are also possible
PIMag® linear motor
Linear motors are electromagnetic direct drives. They dispense with mechanical components in the drivetrain and transfer the drive force directly and friction-free to the motion platform. The drives reach high velocities and accelerations.
Ironless motors are particularly suitable for positioning tasks with the highest demands on precision because there is no undesirable interaction with the permanent magnets. This allows smooth running even at the lowest velocities and at the same time, there is no vibration at high velocities. Nonlinearity in control behavior is avoided and any position can be controlled easily. The drive force can be set freely.
Iron core motors are used when forces and accelerations need to be achieved in a limited installation space. The design with iron cores maximizes the magnetic forces and ensures high thermal stability of the drive.
PIMag®
PI develops proprietary magnetic motors if positioning systems need to achieve specific performance characteristics that cannot be reached by using drive components currently available on the market, for example, to achieve a high force density or a compact design. The motors developed by PI are identified by the PIMag® brand name.
Crossed roller guide
With crossed roller guides, the point contact of the balls in ball guides is replaced by line contact of the hardened rollers. Consequently, they are considerably stiffer and need less preload, which reduces friction and allows smoother running. Crossed roller guides are also distinguished by high guiding accuracy and load capacity. Force-guided rolling element cages prevent cage creep.
Direct position measuring
Position measuring is performed with the highest accuracy directly at the motion platform so that nonlinearity, mechanical play, or elastic deformation have no influence on position measuring.
Application fields
Industry and research. Measuring technology, photonics and precision scanning in semiconductor or medicine technology. /Asset/csm_V-508_588271805f.jpg
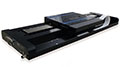
A-110 Air Bearing Linear Slides
(5) Inexpensive high performance nanopositioning stageIdeal for scanning applications or high-precision positioning
Cleanroom compatible
PIglide positioning systems have a magnetic linear motor, magnetically preloaded air bearings and an optical linear encoder: Noncontact and friction-free motion for the highest accuracy and reliability
Application fields
PIglide positioning systems are ideally suited for many high-precision applications such as metrology, photonics, and precision scanning in semiconductor or flat panel display manufacturing.
Thanks to the friction-free motion, no particles are formed, which makes PIglide stages ideal for cleanroom applications. /Asset/csm_A-110_PIC_9106d68816.jpg
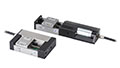
L-505 Miniature Linear Stage / Linear Slide, Motorized
(18) Stepper motor or DC servo motor with and without gearheadCompact linear stage with low-backlash drive screw and ball guides. Directly mountable XY combination. Integrated reference point and limit switches: Hall effect.
The linear stage is available in two design variants:
- Narrow, long variant with direct fixed drive (flange motor).
- Wide, compact variant with belt drive (folded drivetrain). These variants are marked by an "F" at the end of the item number.
Noncontact optical encoders measure the position directly at the platform with the greatest accuracy. Nonlinearity, mechanical play or elastic deformation have no influence on the measurement.
Drive types
- DC motor with or without gearhead
- Stepper motor with or without gearhead
Application fields
Medical industry, Autofocus, Precision microassembly, Biotechnology, Automation /Asset/csm_L-505-02-2er-9_5_46f8d6fc0a.jpg
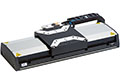
V-417 High-Speed, High Precision Linear Motor Translation Stages, Direct Drive
(7) Incremental or absolute linear encoderCovering strip on the side for protection against particles
Reference-class linear stage
A new linear stage family with linear motors expands PI's product portfolio for industrial solutions. High-performance ironless linear motors, heavy-duty recirculating ball bearings, and precision linear encoders are used. The covering strip on the side and the purge air connection prevent contamination by particles.
Pioneering design
Compared to the competition, the recirculating ball bearings of the V-417 series offer a higher load capacity and allow higher dynamics. The high resolution of the encoders allows improved tracking performance, smaller tracking error, and improved settling times. For maximum flexibility, it is possible to choose between incremental and absolute encoders. Absolute encoders supply explicit position information that enables immediate determination of the position. This means that referencing is not required during switch-on, which increases efficiency and safety during operation.
Linear motors
Linear motors are electromagnetic direct drives. They dispense with mechanical components in the drivetrain and transfer the drive force directly and friction-free to the motion platform. The drives reach high velocities and accelerations. Ironless motors are particularly suitable for positioning tasks with the highest demands on precision because there is no undesirable interaction with the permanent magnets. This allows smooth running even at the lowest velocities and at the same time, there is no vibration at high velocities. Nonlinearity in control behavior is avoided and any position can be controlled easily. The drive force can be set freely.
Application fields
Laser cutting. Scanning. Digital printing. Electronics assembly and inspection. AOI (Automatic Optical Inspection). Automation. Flat screen manufacturing. Applications with high demands on dynamics, precision, smooth scan motion, short settling times, and low tracking error. /Asset/csm_V-417-096211E1-2500_c5e5d83771.jpg
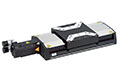
L-417 High-Load Linear Translation Stages / Precision Ball-Screw Slide
(7) Incremental or absolute linear encoder, various resolutionsCovering strip on the side for protection against particles
Powerful linear stage for use in demanding industrial applications
Precision ball screws, high-performance synchronous servo motors, heavy-duty recirculating ball bearings, and precision rotary and linear encoders enable continuous and reliable operation under high load. The optional holding brake allows use as Z axis. The ball screw can be relubricated from the outside without disassembling to ensure high reliability and long lifetimes. It is also possible to integrate into a customer's central lubrication system. The covering strip on the side and the purge air connector prevent contamination by particles.
Pioneering design
The recirculating ball bearings of the L-417 series are designed for high load capacity and dynamics. The high resolution of the motors allows improved tracking performance, smaller tracking error, and improved settling times.
Synchronous servo motor
These motors have high positioning accuracy and high overload capacity over a large rotation speed range. High torque and low inertia ensure the high dynamics of the drives. The long lifetime, high performance, and robustness of these motors allow excellent results in industrial automation applications.
Application fields
Laser cutting. Electronics production. AOI (Automatic Optical Inspection). Automation. Applications with high demands on dynamics, precision, smooth motion, short settling times, and low tracking errors. /Asset/csm_PI-L-417-059232-2500_aa629c82da.jpg
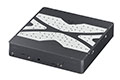
L-741 High Precision Motorized Linear XY-Tables
(6) Highly accurate position measuring with incremental linear encoderNoncontact optical encoders measure the position directly at the platform with the greatest accuracy. Nonlinearity, mechanical play or elastic deformation have no influence on the measurement. Optical limit and reference switches. Further travel ranges on request.
Crossed roller guide
With crossed roller guides, the point contact of the balls in ball guides is replaced by line contact of the hardened rollers. Consequently, they are considerably stiffer and need less preload, which reduces friction and allows smoother running. Crossed roller guides are also distinguished by high guiding accuracy and load capacity. Force-guided rolling element cages prevent cage creep.
Fields of application
Medical industry. Laser cutting. Biotechnology. Metrology. Laser marking. /Asset/csm_L-741-131111_fada1ba831.jpg
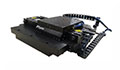
A-311 Planar Air Bearing XY-Table, Linear Scanning XY-Slides,
(5) High-performance, compact XY nanopositioning systemIdeal for scanning applications or high-precision positioning
Cleanroom compatible
Low profile
The high-precision PIglide IS XY planar scanner with air bearing has a flat design and is an alternative to the stacked XY stages. The efficient, compact design saves space in machines with limited installation space.
PIMag® magnetic direct drive
3-phase magnetic direct drives do not use mechanical components in the drivetrain, they transmit the drive force to the motion platform directly and without friction. The drives reach high velocities and accelerations. Ironless motors are particularly suitable for positioning tasks with the highest demands on precision because there is no undesirable interaction with the permanent magnets. This allows smooth running even at the lowest velocities and at the same time, there is no vibration at high velocities. Nonlinearity in control behavior is avoided and any position can be controlled easily. The drive force can be set freely.
Operation with digital controllers from leading manufacturers offers advanced control algorithms for improving the dynamics and error compensation.
Application fields
PIglide positioning systems are ideally suited for high-precision applications, such as inspection systems, laser marking, microscopy or scanning. /Asset/csm_A-311_PIC_2e093ee442.jpg
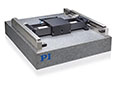
A-322 Planar, Integrated Granite, Air Bearing XY-Table for Scanning
(3) Ideal for scanning applications or high-precision positioningCleanroom compatible
Three performance classes: Base, Plus, and Ultra
PIglide reference-class XY positioning system
The PIglide HS planar scanner has magnetic linear motors, vacuum preload, and an absolute encoder: Contact- and friction-free motion for the highest accuracy and reliability.
The positioning system was designed to maximize the throughput and ensure the highest precision. Flexible coupling of the bridge axis to the gantry axis allows lateral decoupling without sacrificing the stiffness of the system.
The A-322 is coupled with industry-leading controllers and drive modules from ACS that offer superior servo performance, advanced control algorithms to improve dynamic performance and error compensation, and a wide suite of software development tools.
The A-322 series is a starting point for further adaptations. Critical core components such as linear motors, measuring systems, and air bearing assemblies have already been developed, tested, and have proven their capabilities. Depending on the application and requirements of the customer, a variant of the A-322 series forms the ideal starting point for a tailor-made, ultraprecise solution.
Absolute encoder
Absolute encoders supply explicit position information that enables immediate determination of the position. This means that referencing is not required during switch-on, which increases efficiency and safety during operation.
PIMag® magnetic direct drive
3-phase magnetic direct drives do not use mechanical components in the drivetrain, they transmit the drive force to the motion platform directly and without friction. The drives reach high velocities and accelerations. Ironless motors are particularly suitable for positioning tasks with the highest demands on precision because there is no undesirable interaction with the permanent magnets. This allows smooth running even at the lowest velocities and at the same time, there is no vibration at high velocities. Nonlinearity in control behavior is avoided and any position can be controlled easily. The drive force can be set freely.
Long lifetime, cleanroom compatible drag chains
The A-322 has high-quality, long-lasting ribbon cables and pneumatic hoses. Extensive research and development has resulted in an optimized cable management system that enables millions of maintenance-free cycles. Teflon coating ensures low particle formation.
Application fields
PIglide positioning systems are ideally suited for many high-precision applications, such as metrology, photonics, and precision scanning as well as in semiconductor or flat panel display manufacturing.
Thanks to the friction-free motion, no particles are formed, which makes PIglide stages ideal for cleanroom applications. /Asset/csm_A-322_PIC_5651517613.jpg
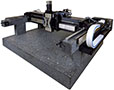
A-341 High Precision XY Gantry / XYZ-Gantry Stage, | Hybrid Bearings
Hybrid guide design with air bearings and recirculating ball bearing guides for high precision with low profile.Hybrid design: Gantry axis with recirculating ball bearing guides, bridge axis with air bearing
Absolute encoder
High-performance ironless linear motors
Various travel ranges. Options and customized adaptations
Flexible modular platform
The A-341 PIglide HGS hybrid gantry system was developed for applications that require overhead motion and long travel ranges.
The A-341 hybrid gantry has a unique hybrid guide design. The bridge axis is equipped with a friction-free guide with air bearings that allow exact control of velocity as well as outstanding repeatability and straightness. The guide with air bearings considerably reduces particle emission over the workspace. The gantry axis is equipped with recirculating ball bearing guides on both sides for robustness and precision in limited installation space.
This combination of different guide technologies means that the A-341 hybrid gantry is ideally suited to applications that are based on the step-and-scan principle and at the same time, require a compact design.
The A-341 is coupled with industry-leading controllers and drive modules from ACS that offer superior servo performance, advanced control algorithms to improve dynamic performance and error compensation, and a wide suite of software development tools.
PIMag® magnetic direct drive
3-phase magnetic direct drives do not use mechanical components in the drivetrain, they transmit the drive force to the motion platform directly and without friction. The drives reach high velocities and accelerations. Ironless motors are particularly suitable for positioning tasks with the highest demands on precision because there is no undesirable interaction with the permanent magnets. This allows smooth running even at the lowest velocities and at the same time, there is no vibration at high velocities. Nonlinearity in control behavior is avoided and any position can be controlled easily. The drive force can be set freely.
Application fields
Scanning, Digital printing, Electronics assembly and inspection, AOI (Automatic Optical Inspection), Automation.
Absolute encoder
Absolute encoders supply explicit position information that enables immediate determination of the position. This means that referencing is not required during switch-on, which increases efficiency and safety during operation. /Asset/csm_A-341_2500px_27b33165e6.jpg
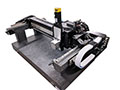
A-351 High Precision XY Gantry / XYZ Gantry System with Linear Motors, Mechanical Bearings
Robust compact design with recirculating ball bearing guides for high load capacity.Overhead moving XY gantry
Precision recirculating ball bearing guides
Absolute encoder
High-performance ironless linear motors
Various travel ranges. Options and customized adaptations
Flexible modular platform
The MGS gantry system has been designed to maximize throughput for applications requiring overhead motion. This stage is ideal for 3D printing, assembly, pick-and-place, alignment, inspection, and industrial automation applications.
The MGS uses preloaded linear mechanical bearings which are designed to provide optimized stiffness and precision. Optional stainless steel guide rails can be delivered.
The gantry axis incorporates dual linear motors and dual linear encoders. Ironless linear motors provide smooth motion and no cogging or attractive forces. The linear motor and linear encoders are noncontact devices, so there is no backlash, wear, or maintenance concerns.
The A-351 is coupled with industry-leading controllers and drive modules from ACS that offer superior servo performance, advanced control algorithms to improve dynamic performance and error compensation, and a wide suite of software development tools.
Application fields
Scanning, Digital printing, Electronics assembly and inspection, AOI (Automatic Optical Inspection), Automation. /Asset/csm_A-351_d87dd33a4a.jpg

L-306 Miniature High Precision Vertical Linear Stage, Motorized
(3) Compact design, multi-axis combinationsStepper motors and closed-loop DC motors
Optional: Linear encoder for direct position measuring
Crossed roller guides
Noncontact reference and limit switches
Compact Z stage, versatile in use
Z stage with compact size due to folded drive with belt drive. Fits onto linear stages with M6 50 mm x 50 mm connection spacing (e.g., L-406).
Crossed roller guide
With crossed roller guides, the point contact of the balls in ball guides is replaced by line contact of the hardened rollers. Consequently, they are considerably stiffer and need less preload, which reduces friction and allows smoother running. Crossed roller guides are also distinguished by high guiding accuracy and load capacity. Force-guided rolling element cages prevent cage creep.
Highly accurate position measuring with incremental linear encoder
Noncontact optical encoders measure the position directly at the platform with the greatest accuracy. Nonlinearity, mechanical play or elastic deformation have no influence on the measurement.
Fields of application
Research, Semiconductor technology, Photonics, Automation /Asset/csm_L-306-011100_c2e59b73ad.jpg
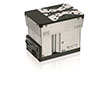
L-310 Precision Motorized Vertical Linear Stage / Z-Stage, Motorized
(4) Compact Multi-Axis Combinations with Linear and Rotation StagesHigh-resolution encoder
DC, BLDC, and stepper motors
Zero-play ball screw
Vacuum-compatible items available
Precision-class Z stage
High guiding accuracy and stiffness due to ball screws and crossed roller guides. Stress-relieved aluminum base for highest stability. Vacuum-compatible product variants on request. Noncontact limit and reference switches (Hall effect). Reference switch with direction sensing in the middle of the travel range.
Minimum incremental motion and slow motion
In conjunction with the SMC Hydra controller, versions with stepper motor and integrated linear encoder (L-310.xASD) achieve repeatable minimum incremental motion in the range of the sensor resolution. The same configuration achieves constant low velocities of a few sensor increments per second.
Highly accurate position measuring with incremental linear encoder
Noncontact optical encoders measure the position directly at the platform with the greatest accuracy. Nonlinearity, mechanical play or elastic deformation have no influence on the measurement.
Application fields
Precision positioning in industry and research, high duty cycles. /Asset/csm_L-310_PIC_c9118711be.jpg

V-611 Compact Direct Drive, High Speed Precision Rotary Tables
(2) High load capacity and long lifetime for industrial applicationsDeep groove ball bearings provide high load capacity and long lifetime
Clear aperture for transmitted-light applications
High velocity and acceleration
PIMag® magnetic direct drive
3-phase magnetic direct drives do not use mechanical components in the drivetrain, they transmit the drive force to the motion platform directly and without friction. The drives reach high velocities and accelerations. Iron core motors are used when forces and accelerations need to be achieved in a limited installation space. The design with iron cores maximizes the magnetic forces and ensures high thermal stability of the drive.
Application fields
Medical industry. Sample inspection. Precision microassembly. Research. Biotechnology. Semiconductor technology. Metrology. Automation. /Asset/csm_PI_V-611-998061_e5f5e8d04d.jpg
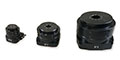
A-62x High Precision Air Bearing Rotary Table, Direct Drive Torque Motors
(6) Friction-free, ideal for indexing, positioning, scanning, measuring technologyCleanroom compatible
Can be mounted vertically or horizontally
The PIglide RM series of motorized rotation stages are designed for accuracy, precision, high stiffness, and ease of use, and can be mounted in any orientation.
Various options can be combined to create a solution ideal for point-to-point indexing or constant velocity scanning.
The RM stages offer superior travel accuracy, flatness, and wobble performance. Because they are friction free and require no maintenance or lubrication, they are ideal for use in cleanrooms.
Absolute encoder (optional)
Absolute encoders supply explicit position information that enables immediate determination of the position. This means that referencing is not required during switch-on, which increases efficiency and safety during operation.
Application fields
Optical alignment, metrology, inspection systems, calibration, scanning. /Asset/csm_A-62x_560dce6cdb.jpg

A-63x Low Profile, Air Bearing Rotary Tables, Direct Drive Torque Motors
(2) Friction-free, motorizedOption for self-locking at rest by magnetic preload
The directly driven low-profile rotation stages of the PIglide RL series are designed for the highest precision with low-profile design. Various options can be combined to create a solution ideal for point-to-point indexing or constant velocity scanning. The RL stages offer superior travel accuracy, flatness, and wobble performance.
Absolute encoder (optional)
Absolute encoders supply explicit position information that enables immediate determination of the position. This means that referencing is not required during switch-on, which increases efficiency and safety during operation.
Application fields
Optical alignment, wafer inspection, wafer alignment, measuring technology, inspection systems, calibration, scanning.
Thanks to the friction-free motion, no particles are formed, which makes PIglide stages ideal for cleanroom applications. /Asset/csm_A-637_PIC_fb527a7bf0.jpg
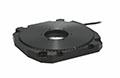
U-651 Ultra-Low Profile Precision Rotary Table with Ultrasonic Piezo Motor
(4) Fast piline® direct drive and central openingPositions larger loads quickly and with precision
Self-locking when switched off: Saves energy and reduces generation of heat
Central aperture for more fields of application
Precision-class rotation stage
PILine® stages are particularly suitable for applications that require fast precision positioning. When switched off, the self-locking drive holds the position of the stage mechanically stable. Energy consumption and heat generation are therefore considerably reduced. Applications with a low duty cycle that are battery-powered or heat-sensitive benefit from these characteristics. The position of the axis is measured by an encoder and an optical reference switch allows reliable repeatable motion. The piezomotor drive principle and its electrical operation are inexpensive and can be customized.
Highly accurate position measuring with incremental encoder
Noncontact optical encoders measure the position directly at the platform with the greatest accuracy. Nonlinearity, mechanical play, or elastic deformation have no influence on the measurement.
Fields of application
Micromanipulation, automation, biotechnology, sample manipulation, sample positioning, optical metrology, vacuum applications to 10-6 hPa (optional)
PILine® ultrasonic piezomotors
An integral part of a PILine® ultrasonic piezomotor is a piezo actuator that is preloaded against a movable, guided runner via a coupling element. The piezoceramic actuator is excited to ultrasonic oscillation by a high-frequency AC voltage between 100 and 200 kHz. Deformation of the actuator leads to periodic diagonal motion of the coupling element relative to the runner. The feed created is a few nanometers per cycle; the high frequencies lead to the high velocities. Preloading the piezoceramic actuator against the runner ensures self-locking of the drive when at rest and switched off.
Crossed roller guide
With crossed roller guides, the point contact of the balls in ball guides is replaced by line contact of the hardened rollers. Consequently, they are considerably stiffer and need less preload, which reduces friction and allows smoother running. Crossed roller guides are also distinguished by high guiding accuracy and load capacity. Force-guided rolling element cages prevent cage creep. /Asset/csm_PI_U-651-04_klein_0063908701.jpg
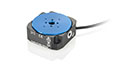
U-628 Miniature Precision Rotary Table, Piezo Motor
Positions loads quickly and with precisionSelf-locking when switched off: Saves energy and reduces generation of heat
Central aperture for more fields of application /Asset/csm_PI_U-628_02_d8da36f5c6.jpg
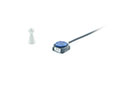
U-622 Ultra-Small Precision Rotary Table, Piezo Motor
Miniature stage with ultrasonic piezo motorExtremely space-saving
Positions small loads quickly and with precision
Self-locking when switched off: Saves energy and reduces generation of heat
Light and low noise
Precision-class rotation stage
PILine® stages are particularly suitable for applications that require fast precision positioning. When switched off, the self-locking drive holds the position of the stage mechanically stable. Energy consumption and heat generation are therefore considerably reduced. Applications with a low duty cycle that are battery-powered or heat-sensitive benefit from these characteristics. The position of the axis is measured by an encoder and an optical reference switch allows reliable repeatable motion. The piezomotor drive principle and its electrical operation are inexpensive and can be customized.
Highly accurate position measuring with incremental encoder
Noncontact optical encoders measure the position directly at the platform with the greatest accuracy. Nonlinearity, mechanical play or elastic deformation have no influence on the measurement.
PILine® ultrasonic piezomotor
An integral part of a PILine® ultrasonic piezomotor is a piezo actuator that is preloaded against a movable, guided runner via a coupling element. The piezoceramic actuator is excited to ultrasonic oscillation by a high-frequency AC voltage between 100 and 200 kHz. Deformation of the actuator leads to periodic diagonal motion of the coupling element relative to the runner. The feed created is a few nanometers per cycle; the high frequencies lead to the high velocities. Preloading the piezoceramic actuator against the runner ensures self-locking of the drive when at rest and switched off.
Fields of application
Micromanipulation, Automation, Biotechnology, Sample manipulation, Sample positioning, optical metrology /Asset/csm_PI_U-622_1180fb125e.jpg

WT-120 Motorized Precision Goniometer Cradle
(3) Long travel range, high loadsOption: Direct position measurement with angle measuring system
Combination with WT-90 with common pivot point
Precision-class goniometer stage
Polished and hardened worm drive with high gear ratio for precision positioning. Two adjustable limit switches.
Can be combined with WT-90 for 2-axis motion with common pivot point.
Application fields
Precision microassembly, Metrology, Photonics, Optical alignment /Asset/csm_WT-120_9baf470bdd.jpg
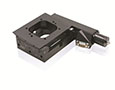
WT-100 Motorized Precision Goniometer Cradle
(4) Option: Direct position measurement with angle measuring systemCombination with WT-85 with common pivot point
Precision-class goniometer stage
Drive with high gear ratio for precision positioning. Two limit switches. Large clear aperture with 60 mm x 25 mm.
Can be combined with WT-85 for 2-axis motion with common pivot point.
Application fields
Precision microassembly, Metrology, Photonics, Optical alignment. /Asset/csm_WT-100_PIC_ebcd45e175.jpg
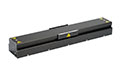
V-855 Compact Motorized High-Speed Linear Modules, High Precision Linear Motors
(4) Highly dynamic, maintenance-free linear motor with velocities up to 4 m/sRobust industrial design for a long lifetime
High-precision incremental or absolute linear encoder
Ideal for gantry systems
Compact industrial design for applications with low power requirements
The V-855 is a heavy-duty and highly dynamic linear stage for industrial applications. Its design is consistently geared to demanding industrial conditions and it is characterized by high stiffness and the use of high-quality components: recirculating ball bearing guides, 3-phase linear motor, incremental or absolute linear encoder. The high resolution of the encoders allows an excellent tracking performance, small tracking errors, and short settling times. Industry-compatible connectors offer a fast and secure connectivity. The optional motion platform offers versatile assembly options with a triple M6 hole pattern.
Linear motor with direct drive
3-phase magnetic direct drives do not use mechanical components in the drivetrain, they transmit the drive force to the motion platform directly and without friction. The drives reach high velocities and accelerations. Ironless motors are particularly suitable for positioning tasks with the highest demands on precision because there is no undesirable interaction with the permanent magnets. This allows smooth running even at the lowest velocities and at the same time, there is no vibration at high velocities. Nonlinearity in control behavior is avoided and any position can be controlled easily. The drive force can be set freely.
Application fields
Electronics assembly: Sensor and camera assembly. Noncontact inspection, X-ray inspection, and AOI (automated optical inspection). Sensor and ultrasonic tests. Semiconductor manufacturing: Wafer processing and inspection. Laser machining: Laser welding. Highly dynamic applications in precision automation, smooth scan motion, minimum tracking errors, and short settling times. /Asset/csm_V-855_merged-tif_Bilder-Web_196244dcfc.jpg
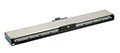
V-817 Fast, High-Precision Motorized Linear Stages with 3-Phase Linear Motors
(4) Highly dynamic, maintenance-free linear motor and high precision incremental linear encoderRobust industrial design for a long lifetime
Fast integration thanks to reference edge, easily XY stackable
Creation and delivery of test reports as a standard
Industrial design for high performance and high load
With the V-817, PI has a linear stage in its portfolio for industrial solutions that has a high load capacity and high dynamics. Its design is consistently geared to demanding industrial conditions and it is characterized by high stiffness and the use of high-quality components: Recirculating ball bearing guides, 3-phase linear motor, incremental linear encoder. The high resolution of the encoders allows an excellent tracking performance, small tracking errors, and short settling times. Industry-compatible connectors offer a fast and secure connectivity. The optional motion platform offers versatile assembly options with a triple M6 hole pattern. A particularly low overall height is achieved without this platform, which offers advantages especially in XY combinations.
Linear motor with direct drive
3-phase magnetic direct drives do not use mechanical components in the drivetrain, they transmit the drive force to the motion platform directly and without friction. The drives reach high velocities and accelerations. Ironless motors are particularly suitable for positioning tasks with the highest demands on precision because there is no undesirable interaction with the permanent magnets. This allows smooth running even at the lowest velocities and at the same time, there is no vibration at high velocities. Nonlinearity in control behavior is avoided and any position can be controlled easily. The drive force can be set freely.
Fully integrated multi-axis systems
The V-817 linear stages are perfectly suited for being integrated into complex systems. Therefore, PI offers integrated XY or XYZ multi-axis systems with the suitable controller as well as accessories such as a granite base, machine frame, mounting adapter, cable set, and appropriate software support. For requests regarding multi-axis systems, contact our sales department.
Application fields
Electronics assembly: Sensor and camera assembly. Noncontact inspection, X-ray inspection, and AOI (automated optical inspection). Sensor and ultrasonic tests. Semiconductor manufacturing: Wafer processing and inspection. Laser machining: Laser welding. Highly dynamic applications in precision automation, smooth scan motion, minimum tracking errors, and short settling times. /Asset/csm_V-817-336211E0-tif_Bilder-Web_f4dd3928ba.jpg